L’industrie 4.0 : La quatrième révolution industrielle, qui améliore la sécurité et la qualité de la production en usine
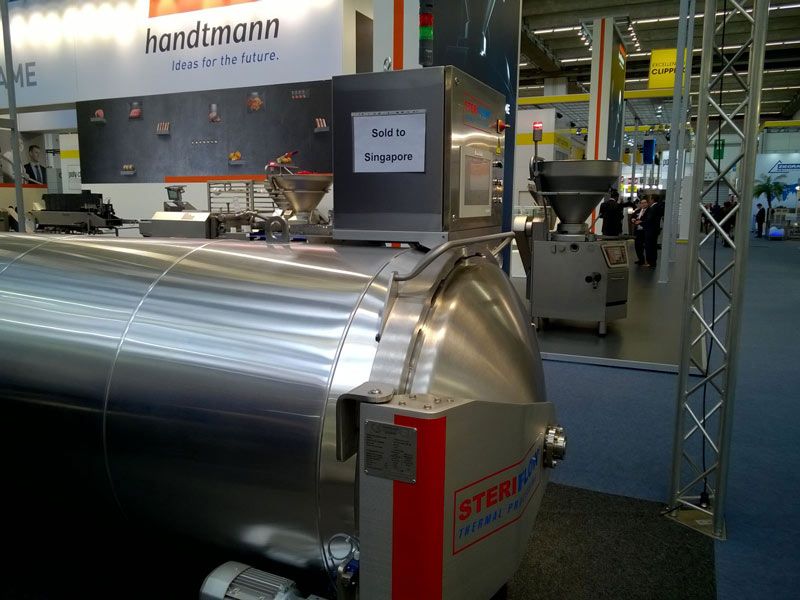
Industrie 4.0
Avec l’arrivée de la numérisation, les industries deviennent de plus en plus compétitives et proposent des produits et services personnalisés. L’industrie du futur est en marche vers un système global interconnecté. La communication permanente entre les machines et systèmes (ERP, etc) garantit une amélioration croissante de la production.
Comment répondre aux exigences dans la production industrielle
À la fin des années 80, les entreprises de transformation des aliments avaient besoin d’un dispositif électronique pour contrôler deux paramètres principaux : la durée et la température. La réponse à cette demande fut le développement d’un automate programmé dont la tâche consistait uniquement à gérer des cycles. Quelques années plus tard, pour répondre aux exigences de production, de nouveaux paramètres étaient ajoutés aux automates : gestion de la valeur F0, distorsion de l’emballage flexible, rapports de cycle, connexion réseau, gestion de la ligne de stérilisation et enfin intégration dans une ligne de production complète permettant au processeur de tout gérer à partir d’une seule interface.
Les nouvelles technologies développées étaient en fait des adaptations de processus existants. Le seul objectif était d’améliorer et de mieux contrôler le traitement thermique. Forts de cette expérience, les industriels préparent l’avenir avec le déploiement de la gestion du Big Data et de l’industrie intelligente. Le développement de l’industrie 4.0 repose sur 5 axes principaux, à savoir : la maintenance et la calibration, la qualité et la traçabilité, la consommation d’énergie, la surveillance et le contrôle et la cybersécurité. L’objectif n’est pas seulement d’améliorer l’expérience utilisateur. Il s’agit d’améliorer considérablement le fragile équilibre entre sécurité et qualité des produits.
Quels sont les risques encourus par les industriels avec le déploiement de l’industrie 4.0 ?
La sensibilisation des industriels quant aux risques encourus à la digitalisation de leur processus de production est importante. Des cyberattaques peuvent mettre en péril une société. Toutes les entreprises peu importe le secteur d’activité peuvent subir une attaque. La première est une attaque de la part de cyber assaillants qui tentent de récupérer des informations confidentielles. Des cyberattaques peuvent détruire un système. Des tentatives de sabotage à l’aide de virus entrainent des dysfonctionnements et parfois même un détraquage des machines. Des campagnes de ransomware ou de DDOS (Distributed Denial of Service), qui visent à rendre un serveur, un service ou une infrastructure indisponible, peuvent être responsables de l’immobilisation de chaînes complètes de fabrication. Les systèmes pilotant les machines sont rendus indisponibles.
Comment se protéger des cyberattaques ?
Il est essentiel de mettre en place d’une stratégie de cybersécurité. Effectuer une veille, un audit des risques potentiels, cartographier les systèmes mis en place ainsi que répertorier les droits d’accès des salariés et des sous-traitants est obligatoire. Sur un plan plus technique, il est important de protéger le système informatique avec le déploiement de Firewalls. Il est préférable de faire surveiller son activité informatique par un organisme spécialisé tel qu’un SOC (Security Operations Center) afin d’être alerté de tout incident ou attaque.
La digitalisation permet l’évolution des processus de production
Puces RFID, Intelligence artificielle, réalité augmentée et analyse de données, toutes ces nouvelles technologies offrent des capacités de mémorisation plus grande avec des puissances de calcul plus élevées à moindre coût.
En se modernisant, s’automatisant et se digitalisant, la place de l’humain dans la chaine a évolué. L’homme ne produit plus mais accompagne et permet de faire fonctionner le processus industriel. Ses interventions sont diverses et demandent une polyvalence pour le paramétrage et le contrôle des machines. La digitalisation est une aide quant à la traçabilité des processus. Les tâches de maintenance sont facilitées, il est plus facile et rapide de trouver l’origine de défaillance.
Vous souhaitez en savoir plus sur l’industrie du futur et Steriflow ? Retrouvez-nous le mercredi 27 février 2019 lors d’une conférence « Comment la digitalisation améliore le processus de traitement thermique » à l’IFTPS 2019. Intervention de Pierrick Salvy lors de l’annuel rendez-vous des professionnels du traitement thermique à San Antonio, Texas, USA.