High flow cascading water for the treatment of a heat sensitive product: albumin
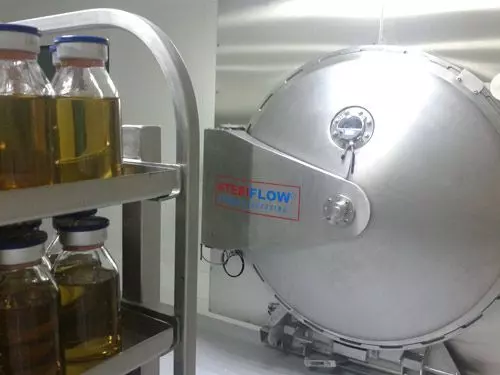
High flow cascading water : the adequate solution for heat sensitive products such as albumin treatment
Therapeutic solutions make it possible to use natural drugs to treat patients reached by serious diseases medically. Albumin is a protein produced by the liver and carries substances in the blood (electrolytes, hormones, coagulation factors …). For manufacturing human albumin solutions, pasteurization is a compulsory step in order to preserve the protein.
The albumin treatment’s process by pasteurization
The albumin treatment’s process goes through an appropriate pasteurization cycle. The temperature must be maintained at 60 ° C during a 10 to 13 hours stage. The accuracy of the control temperature is of 60 ° C ± 0.25 ° C. This necessary accuracy is so that the products do not undergo a temperature variation that could make them unusable, inefficient or even dangerous. STERIFLOW has developed a measurement chain with specific PT100 probes, electrical input / output modules and its MPI Expert control system to ensure that the measurement uncertainty is as low as possible.The cascading water’s pasteurization technology invented by STERIFLOW ensures the best temperature homogenization of the product vs the air-steam process.
STERIFLOW cascading water process, tested and approved for natural drugs’s pasteurization
An experiment was conducted by a biopharmaceutical company wishing to invest in a new albumin pasteurization solution. A cycle test demonstrated the accuracy of the hardware and control system developed for this application. 120 probes placed in the tank during the 10 hours required for the pasteurization cycle revealed a difference of less than 0.2 ° C between each probe. During a pasteurization’s cycle, it is essential to have complete control over the temperature. Safety allows direct control of temperature variations (the machine is secured above 60.5 ° C).
The water cascading process’s by STERIFLOW
Each cycle is automatically performed according to the parameters stored in the MPI Expert individual microprocessor programmer. A complete cycle lasts approximately 23 hours. At first, the process water flows over the products to be treated with a high flow rate for the pasteurization phase at 60 ° C. The products are then dried in the air for ten hours. Throughout the cycle, the back pressure is controlled by injection or purge of compressed air inside the vessel through two automatic valves. A light indicates the end of the cycle, thus allowing the opening of the door. The STERIFLOW is unloaded and ready for a new cycle.